A tire manufacturer in the southern United States was facing issues in their eight water baths that are used to cool the rubber after it has been extruded. The water chemistry in the baths must be maintained within the machine and equipment standards (MES), so that the finished rubber maintains its strength. Historically, the manufacturer had been trying to maintain these parameters manually, which presented challenges in keeping the components consistent, such as the water baths being maintained the MES standards.
To reach suitable cooling water quality, the process includes chemical treatment to combat microbiological growth, water filtration to control total suspended solids (TSS), pH control and automatic water exchange to effect conductivity. Per the MES, microbiological growth can be confirmed visually and should not surpass 100 relative light units (RLU). The acceptable TSS is at thirty milligrams per liter (mg/L) after flowing through a filter trap, pre-filter, and final filter. The conductivity must be under 1000 microsiemens per centimeter (μS/cm) to maintain an acceptable level of water discharge and replacement. The water baths include sprays that contact the rubber as it comes out of the extruder, and then the section where the rubber is submerged in the bath water for further cooling.
The third-party company, Enkrott, had developed an automated equipment package that included sensors and other monitoring equipment and asked Kurita America to provide both the chemistry and on-site support. Kurita and the equipment provider’s goal was to filter the water and reduce suspended solids, control pH, and limit bacteria and oxidation reduction potential (ORP) to control growth in the extrusion baths. Facilities that deal with microorganism growth within the cooling circuit can see it in two forms: free-floating (planktonic bacteria) and anchored (sessile bacteria or biofilm).
The Enkrott system utilized various components to meet the MES. Two of the components required the use of chemistry: pH and ORP. It is essential to maintain the pH of the cooling water within the given quality limit values in order to preserve a certain tackiness of the rubber components for further downstream processing. Also, it is required that the ORP of the water be monitored, and the disinfectant automatically dosed into the system depending on the set ORP value. As a general rule, the base ORP of the water should be measured and then 150 to 200 millivolts (mV) added. This range is an indication or starting point and can be adjusted depending on the observed condition after a longer period of consistent dosing. If there is already good control, then it can also be possible to reduce the target values to optimize dosing and minimize cost.
In order to reach the pH value, an acid-dosing system is employed for the water station. The pH of the water is monitored by two pH measuring probes, which then send a signal to the acid dosing pump. The acid dosing system is to be dosed automatically and continuously based on the readings from the pH probes to the required value. Kurita America was able to quickly solve the pH issue with the use of AcidPro. Instead of the plant personnel having to handle this product without specific training, Kurita America introduced the EZ Feed delivery system.
Kurita America’s EZ Feed is a drumless delivery, hands-free chemical storage system that is an operator-friendly solution designed to reduce the hazards and liability associated with chemical programs. Kurita America provides base tanks that are built to Department of Transportation UN Standards by an ISO 9001 certified manufacturing plant, which are filled by trained Kurita America delivery specialists. Overall, the EZ Feed system prevents loss of product feed, removes drum disposal costs, eliminates operator handling, and increases operational efficiencies.
After the facility selected the EZ Feed system for chemical delivery and pH control, Kurita America began looking for chlorine dioxide alternatives. Chlorine dioxide is very reactive, and handling and storage of this material is very challenging. After approval from the tire manufacturer, Kurita America initiated a comparison of chlorine dioxide and sodium hypochlorite with a focus on employee safety. After running the line for four months using chlorine dioxide and collecting data, the systems were transitioned to Biotrol 12.5, which is a fast-acting biocide solution for cooling water and evaporator condensers, wastewater, and food washing applications. During the evaluation period, Kurita America’s representative was on-site every two weeks to ensure the evaluation was meeting expectations and maintaining MES.
Immediate results were apparent during the comparison of the chlorine dioxide and the Biotrol 12.5. The overall bacteria count remains consistent with Kurita America’s Biotrol 12.5 treatment. With both acid and biocide in the EZ Feed delivery system, the plant can maintain MES with no chemical handling by plant personnel. This ensures that continuous feed is maintained, and no facility employees are exposed to chemicals. Because of the EZ Feed system, there has been a significant improvement in plant safety from potential spills or chemical burns. Kurita America continues to work with the company to meet their parameters.
Kurita America will continue to provide the necessary chemicals, support, and monitoring to ensure the water in the baths are always within the specified MES.
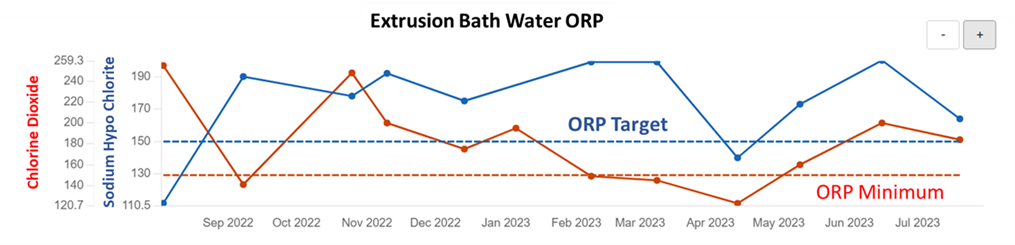